智造带来的变革和机遇
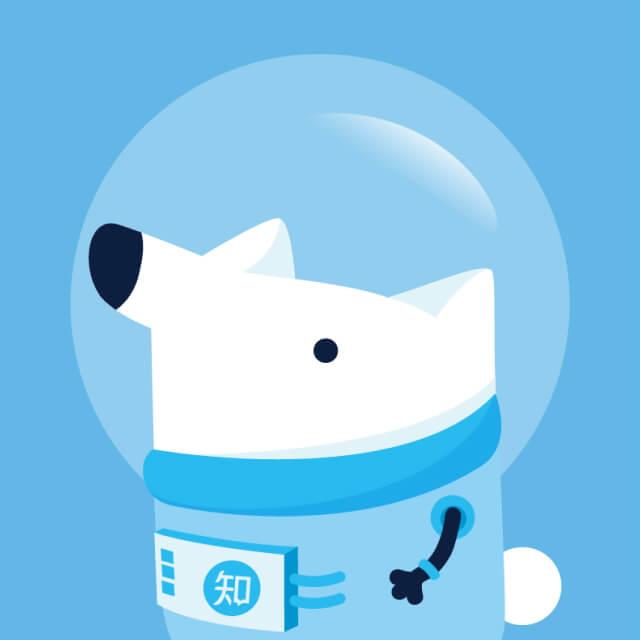
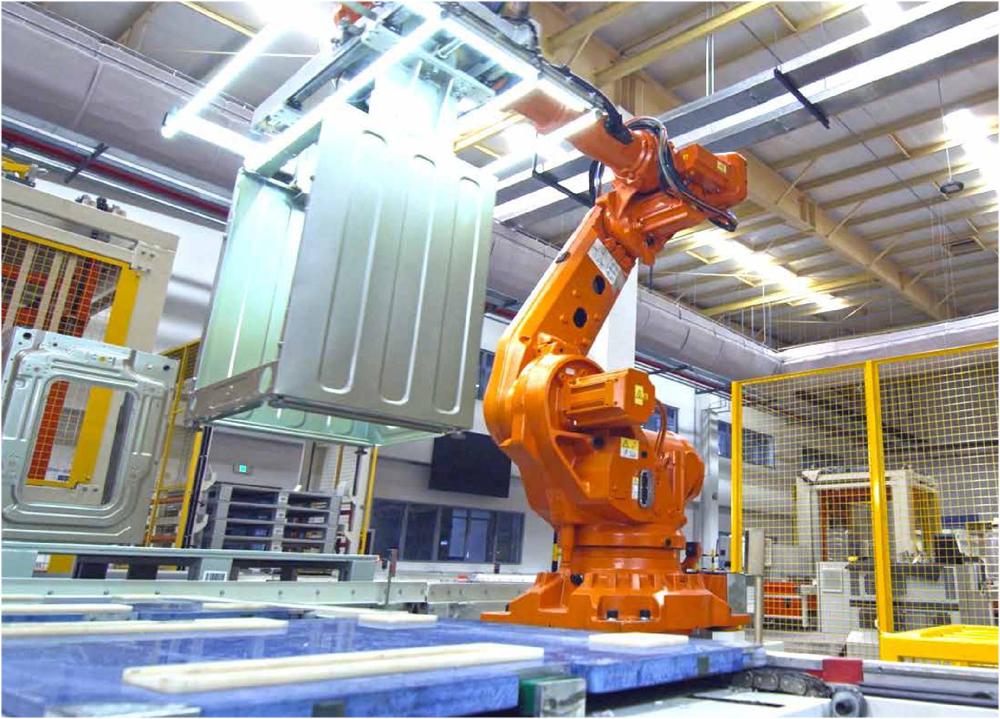
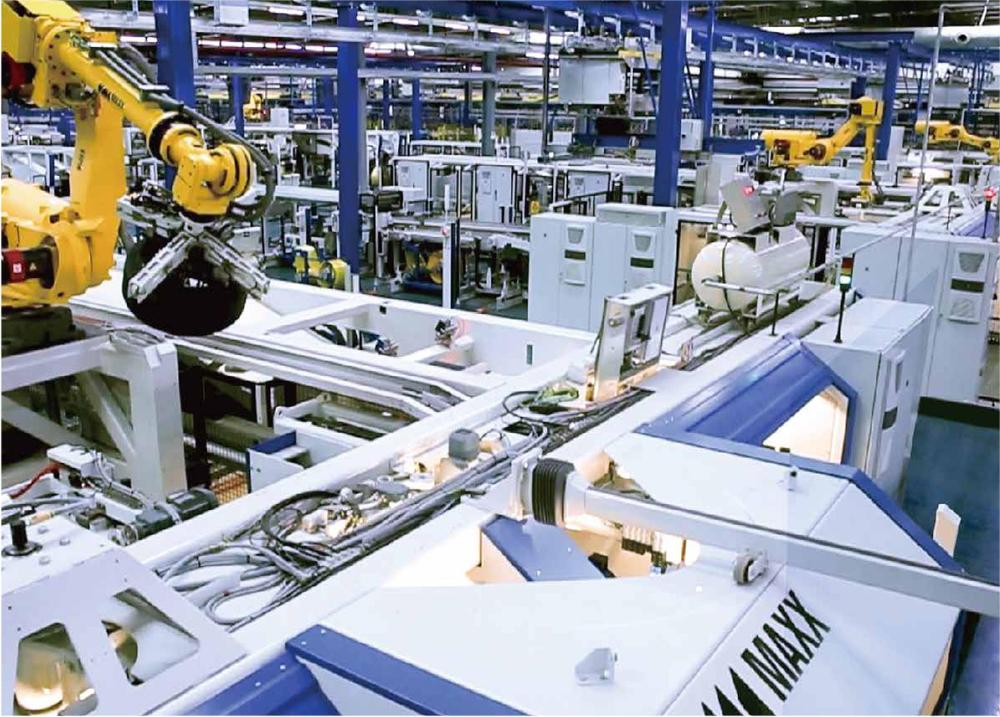
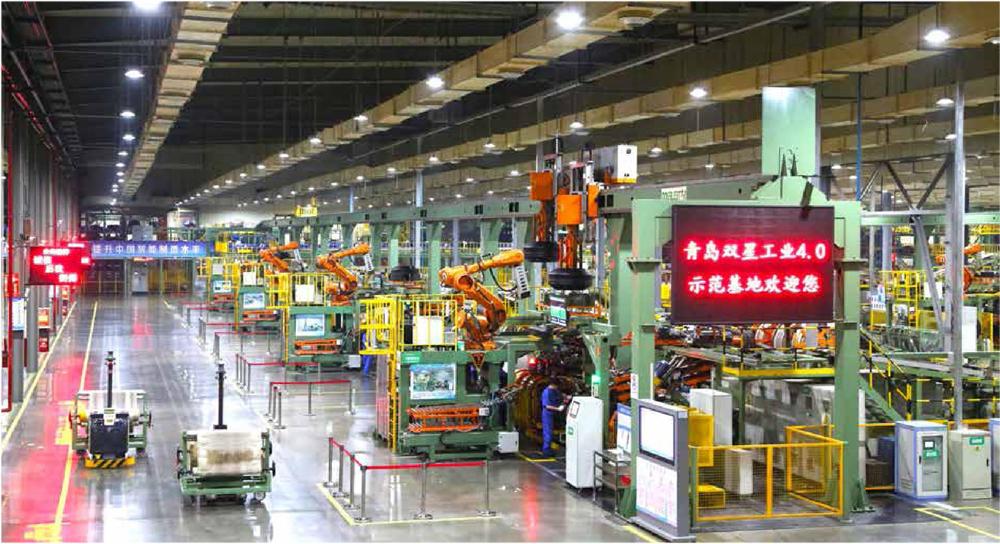
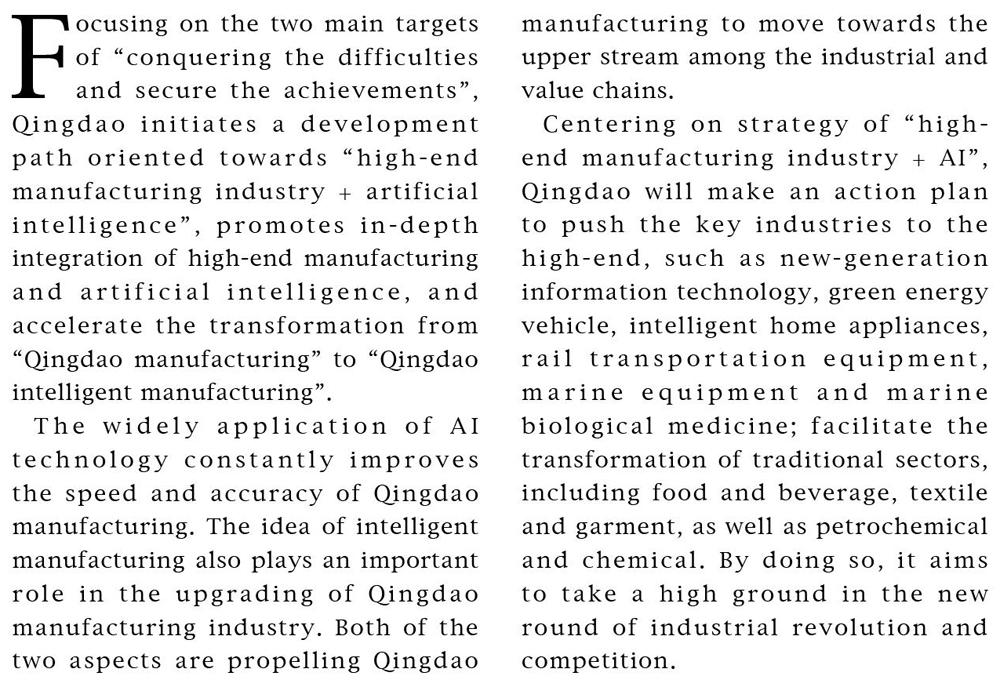
发起一个又一个攻势,炸掉一个又一个「碉堡」,拿下一个又一个「山头」
近日,青岛迅速发起海洋攻势、「双招双引」攻势、交通基础设施建设攻势、军民融合发展攻势、突破平度莱西攻势、东北亚金融贸易中心建设攻势、「高端制造业 + 人工智能」攻势、壮大民营经济攻势、科技创新城建设攻势、城市品质改善提升攻势、国际时尚城建设攻势、高效青岛建设攻势、「平安青岛」建设攻势等 15 个攻势,立体、综合、全方位地「搞活一座城」,整合全球优质要素资源,真正昂起龙头,打造山东面向世界开放发展的桥头堡,成为国家高质量开放发展的重要支点。
聚焦「攻山头、稳阵地」两条主线,青岛发起「高端制造业十人工智能」攻势,推动高端制造与人工智能深度融合,加快从「青岛制造」向「青岛智造」迈进。实际上,智能制造带给企业的变革和机遇,已经让「先行者」踏上追梦腾飞之旅。
海尔互联工厂重新定义中国制造
在物联网技术飞速发展的当下,智能制造已不是简单得通过智能制造设备提升生产效率,而是能将用户需求融入到全流程的互联工厂体系中。在位于青岛西海岸新区中德生态园的海尔洗衣机互联工厂,一排排智能化设备整齐排列,从一张铁皮变成一台洗衣机仅需要 38 分钟,整个工厂 9 大关键工序 108 个检测点全部实现智能自动检测、检测数据全部实现 SPC 智能控制,全流程可追溯,实现产品全过程质量防差错管理,多项人工智能技术的运用,不仅提高了生产效率,产品的品质也更有保证。
相比传统工厂,海尔互联工厂创新的人工智能检测等多项行业领先技术,实现全流程数据链贯通,用户定单通过 COSMOPlat 可以直达工厂,工厂直发用户,真正做到用户定单驱动生产,极大的缩短了用户定单交付周期,实现高精度下的高效率。
从布局第一座互联工厂开始,海尔将 30 多年的制造经验软化、云化、产品化,构建以用户体验为中心的大规模定制平台——COSMOPlat,通过这一平台的内部应用实践,目前海尔在中国已拥有 11 座互联工厂正式投入生产运营。除了实现海尔自身转型外,COSMOPlat 正从家电行业向汽车、建陶、服装、农业、机械等行业延伸,复制形成了 15 个行业生态,并在全球 20 多个国家复制推广。以海尔洗衣机互联工厂为例,它是目前全球生产规模最大、智能化最高、柔性化最强的洗衣机互联工厂。通过 COSMOPlat 平台打通了海尔内部的交互、设计、营销、采购、生产、物流、服务全流程七大节点,在 COSMOPlat 平台上每个节点与用户都可以实现零距离的交互,实现用户需求与制造体系的无缝对接,为用户提供真正需要的高质量产品,满足用户的最佳体验。在用户下单后,通过 COSMOPlat 平台,互联工厂全流程会实时接收到用户的订单信息进行智能排产,同时用户定单信息可以并行传达至模块商进行模块采购,工厂内部也会根据用户的订单来安排模块加工及柔性总装,对于标准模块采用大规模流水线式的生产,对于可变模块采用柔性单元线的生产模式,真正做到用户定单驱动工厂生产。
据悉,作为目前全球规模最大、柔性最高的滚筒洗衣机模块化制造基地,海尔洗衣机互联工厂具备 400 余种型号产品的制造能力,产品覆盖 5 公斤至 13 公斤不同容积的全系列产品,包括纤见洗衣机、双子云裳洗衣机、直驱洗衣机等。其中,海尔直驱洗衣机原创直驱变频科技,打破传统皮带电机束缚,从源头降噪,实现极致安静平稳运行。海尔直驱系列洗衣机自上市以来深受用户认可,引领行业「安静洗」潮流。除安静洗优势外,海尔直驱洗衣机还创新 601 毫米大筒径,极大满足用户大件衣物的洗涤需求,引领行业「大容量」趋势。
业内人士认为,海尔互联工厂可实现用户、产品、设备、生产线之间的实时互联,将生产出更多以海尔直驱系列洗衣机为代表的能精准满足用户需求的产品。届时,从消费者的一个概念到最终通过智能物流送货上门的产品,都可以在海尔互联工厂中完成。
在「人单合一」模式指导下,海尔互联工厂基于 COSMOPlat 大规模定制模式,让用户全程参与所有环节,也让用户从原来单纯的消费者转变为「产消者」,同时为行业企业探索智能制造领域提供有益借鉴。
双星加速智慧转型引领世界轮胎智能制造
人工智能技术的应用,不断提高着青岛制造的速度与精度。具有 98 年历史的老国有橡胶企业双星,是山东省轮胎行业目前惟一一家国有主板上市公司,也是新一届中国橡胶工业协会轮胎分会理事长单位,曾创出中国鞋业历史上第一个着名品牌。2008 年,双星集团全面转行到轮胎产业,目前已经形成了集轮胎、智能装备、工业智能物流(含机器人)、废旧橡胶绿色生态循环利用等四大产业体系。
近年来,开启「二次创业、创双星世界名牌」新征程的双星,抓住全球第四次工业革命的契机,加速企业智慧转型,率先建立了全球轮胎行业第一个全流程「工业 4.0」智能化工厂,成为 5 年来中国所有企业中惟一一家被国家工信部授予「品牌培育」「技术创新」「质量标杆」「智能制造」「绿色制造」「服务转型」全产业链试点示范的企业,被誉为是「中国轮胎智能制造的引领者」,也是中国轮胎历史上惟——家被评为「全国先进生产力典范企业」的企业。双星品牌已连续 4 年荣登「亚洲品牌 500 强」中国轮胎第一名和「中国 500 最具价值品牌」轮胎行业榜。2018 年 8 月被列入国企改革「双百行动」计划。为了发展成为具有更大规模的国际化轮胎企业,双星于 2018 年 7 月 6 日正式控股锦湖轮胎,一举成为全球前十、中国最大的轮胎企业。双方协同从用户需求的引领者做起,创造全球最受尊重的轮胎品牌。
近年来,双星整合全球顶尖的「工业 4.0」专家和伙伴资源,集成全球最先进的信息通讯技术、数字控制技术和智能装备技术,率先建立了全球轮胎行业第一个全流程「工业 4.0」智能化工厂,融「产品定制化、企业互联化、制造智能化」于一体,搭建了一个由用户(订单)指挥、数据驱动、软件运行的智能生态系统。生产线上的设备包括 11 种、300 余台智能机器人,其中 80% 是双星自行设计和生产的,各式智能机器人有条不紊地进行着炼胶、敷贴和成型等工作,实现了产品定制化、企业互联化、制造智能化人工效率提高了近 3 倍,不良率降低 80% 以上,企业由「汗水型」转型到「智慧型」,被称为「中国轮胎智能制造的引领者」。
双星的全流程「工业 4.0」智能化工厂中采用了双星独创的 MEP 智能信息匹配系统,实现物、人、设备、位置的信息智能匹配,解决了全球以液体或粉体为原料的制造企业无法全流程实现智能制造的难题;工厂采用的 APS 智能排产系统,被德国西门子公司专家称为「全球第二家将 AIDS 应用到实际生产中的轮胎企业,走在了世界前列,引领了世界轮胎智能制造的方向」。与此同时,双星率先打造轮胎工业 4.0 样板工厂,为行业转型升级提供服务。2018 年 8 月,国务院国资委公布的国企改革「双百行动」企业名单,双星位列其中,为国有企业的深入改革和创新发展树立典范。
通过技术创新和产业升级,双星不仅加快企业的智能化改造,还拥有了颠覆性的新技术、新业态、新模式,催生出前景广阔的智能装备、工业智能物流和废旧橡胶绿色生态循环利用三大新产业。双星智能装备和工业机器人为轮胎及其他行业的转型升级和新旧动能转换提供服务和保障。2014 年以来,双星与德国西门子共同成立轮胎行业惟一的「工业 4.0」创新中心,打造行业符合工业 4.0 标准的智能化生产方案;与瑞典 ABB 联合成立机器人应用研发技术中心,研发制造工业机器人应用技术;与韩国现代签署协议共同成立合资公司,开发智能物流关键装备与核心技术。通过与全球最优秀的公司开展合作,双星加速轮胎智能制造装备研发,助力轮胎行业转型升级。而废旧轮胎绿色生态循环利用技术解决了全球废旧橡胶循环利用 17 大难题,真正实现了「零排放、零残留、零污染、全利用」,变「黑污染」为「黑黄金」,被评价为「两山」理念的典型实践、「为国分忧、为民造福」的好项目,助力建设无废旧橡胶绿色生态文明城市。
赛轮金宇振奋中国力量智能制造助力弯道超车
在大量运用人工智能技术的同时,智能制造理念也在青岛制造业迈向高端的过程中发挥着重要作用。
轮胎是国家的重要战略物资和安全产品,目前正向智能、绿色、安全等方向发展,提升轮胎生产和产品智能化、信息化应用是实现轮胎企业转型和优化升级的最佳路径。在轮胎生产制造过程和产品中应用 RFID 和信息化技术是达到上述目标的重要手段,目前只有米其林等极少数国际轮胎制造企业在研究和应用上述技术,而国内轮胎企业中赛轮集团率先研制生产带「电子身份证」的轮胎
RFID 智能轮胎。
成立于 2002 年的赛轮集团股份有限公司,是中国首家 A 股上市民营轮胎企业,集轮胎研发、生产、销售和服务为一体,年营业收入超过 130 亿元,总资产逾 150 亿元。集团在青岛、东营、沈阳及越南建有现代化轮胎制造工厂,在加拿大、德国等地设有服务于美洲和欧洲等区域的销售网络与物流中心,产品畅销欧、美、亚、非等 100 多个国家和地区.为全球 500 多个客户提供服务。2018 年,赛轮轮胎以 295.16 亿元品牌价值入选由世界品牌实验室发布的「中国 500 最具价值品牌榜单」,目前集团半钢子午线轮胎出口额连续 5 年位列中国轮胎企业第一。
集团率先建成国内首家子午线轮胎信息化生产示范基地,并先后获批「两化融合管理体系贯标试点企业」「国家首批智能制造试点示范企业」「国家工业互联网试点示范企业」「国家物联网集成创新与融合应用示范企业」「国家服务型制造示范企业」「青岛市首批互联网工业三个五」试点示范企业等,为工信部「智能制造综合标准化与新模式应用项目试验验证基地」;承建「国家橡胶与轮胎工程技术研究中心科研示范基地」「国家博士后科研工作站」「中国首批轮胎资源循环利用示范基地」等,并承建了「轮胎先进装备与关键材料国家工程实验室」「山东省巨型工程子午胎与新材料应用工程研究中心」等科技创新平台;同时联合中国一汽建设国内领先的智能网联汽车和轮胎试验场,带动行业向产业链中高端迈进。
RFID 智能轮胎是将 RFID 应用到轮胎内部,使其与轮胎生产、使用、翻新等信息进行绑定,建立轮胎全生命周期管理和追溯,形成从原材料、轮胎成品、轮胎销售、三包理赔直到轮胎报废的完整质量追溯体系,实现了基于 RFID 技术的轮胎原材料、密炼、半制品、成型、硫化、质检、仓储以及销售、三包理赔、翻新等环节的全流程信息管理系统,真正实现了业务流、信息流与物流的统一。智能轮胎的研发实现了轮胎全生命周期的实时、动态、可追溯管理,提高了轮胎质量的均一性,提升了轮胎企业运行效率与效益;成果极大地推动信息化技术在子午线轮胎生产中的应用,以技术先进性、功能适用性、行业服务性优势,提高了轮胎生产、物流、销售过程的智能化水平,从根本上改变了传统企业的管理方式,使轮胎企业生产效率提高 5% 以上,产品合格率提升 3% 以上,能耗降低 7% 以上,退赔率降低 4% 以上,推动了中国轮胎产业两化融合开始由单项应用向集成提升、整合创新阶段迈进,为中国国制造业向智能型、服务型转变提供示范与借鉴。
赛轮集团智能工厂立足于橡胶轮胎行业,依托于生产装备高度的信息互联和信息系统的实时采集,集 RFID 技术、视觉检测技术、激光传感器等无线感知技术于一体,融合数据挖掘、物联网、自动化仓储物流、机器人以及智能化生产装备等先进技术,全面覆盖轮胎制造生产流程,在实现生产设备、生产信息、过程管理、企业决策的纵向交互的同时,实现生产过程各工艺流程横向交互,从而实现纵横贯通的综合集成优化的轮胎智能制造解决方案,最终搭建橡胶轮胎智能工厂智能研发设计体系、智能生产制造体系、智能物流仓储体系、智能营销服务全生命周期协同运营体系,形成面向橡胶轮胎企业的智能制造应用新模式,实现智能化管理及优化,提供各环节资源最佳配置,达到生产节奏和效率的最佳匹配;同时利用大数据云平台进行感知、分析、推理、预警、决策与控制,实现轮胎产品需求的动态响应、迅速开发以及对生产和供应链网络实时优化,为传统轮胎制造工厂提供智能制造的最佳实践。
赛轮集团通过集成制造技术与数字技术,推进轮胎装备产业智慧化,引领全球轮胎智能化产业升级。通过在行业内率先实施轮胎制造全过程智能化技术改造,成为中国轮胎行业智能制造示范企业;通过搭建工业大数据及云服务互联网工业平台,使生产效率提升 85% 以上,人员节省 70% 以上,显着提高了产品质量均一性,并降低产品不良率和生产运营成本,实现轮胎智能制造的全生命周期管理升级,促进传统轮胎产业向智能制造转型升级。
森麒麟不断自我强 44:深耕轮胎智能制造领域
青岛森麒麟轮胎股份有限公司成立于 2007 年 12 月,公司致力于绿色、安全、高品质、高性能半钢子午线轮胎及航空轮胎的研发、生产与销售,已建成中国青岛、泰国罗勇两大轮胎智造基地,其中青岛设计产能 1200 万条半钢子午线轮胎,罗勇设计产能 1000 万条半钢子午线轮胎,其高性能半钢子午线轮胎多次在国际权威测试中成绩名列前茅,比肩国际一线知名品牌。2018 年在国内轮胎企业中森麒麟人均销售收入位居首位,并稳居全球行业前列,半钢子午线轮胎产销量也排名前 5。
2014 年,森麒麟率先建成中国第一家轮胎智能工厂,积极响应国家「一带一路」的倡议 2015 年又在泰国投资建成全球领先的轮胎智能工厂;作为轮胎产业转型典范企业,森麒麟智能制造模式具备有世界领先水准,实现企业「两化融合」,推动轮胎行业智能制造设计标准化,促进行业新旧动能转换,彰显出行业示范效应。并且,森麒麟「智造」成果入选「2016 年智能制造综合标准化与新模式应用」「2017 年智能制造试点示范项目」「2018 年制造业与互联网融合发展试点示范项目」,连续 3 年成为国家工信部上述示范项目中惟一入选的轮胎企业。
森麒麟轮胎智能工厂以创新驱动,将机器人技术、工业互联网(IOT)技术、大数据分析技术、云计算技术、人工智能技术和制造业深度融合,促使多维度信息互联互通,实现生产全流程的「自动化、信息化、智能化、数字化、可视化、可溯化」,同时,创新性导入「扁平化架构、平行化管理」管理理念,打造出森麒麟独具特色的智能制造新模式,真正实现企业「精益运营」,单机生产效率提升 50%,产品综合合格率达到 99.9%,生产用工减少 75%,厂房建筑面积节约 50%。
人工智能技术和智能制造理念的应用,正推动青岛制造走向产业链、价值链高端。围绕「高端制造业 + 人工智能」攻势,青岛将推动新一代信息技术、新能源汽车、高端智能家电、轨道交通装备、船舶海工装备、海洋生物医药等重点产业迈向高端,促进食品饮料、纺织服装、石化化工等传统产业转型升级,抢占新一轮产业变革与竞争的制高点。
作者 王欣